7月31日,贵州轮胎(000589.SZ)发布公告称,拟投资建设两个轮胎大项目,继续推动“双基地”发展战略顺利实施。
在国内生产基地,贵州轮胎接下来计划投资23.01亿元,用于建设位于贵阳市修文县扎佐工业园的年产300万套高性能全钢子午线轮胎智能制造项目,建设周期3年。建设完成达产后,预计可实现年均营业收入27.68亿元。贵州轮胎称,此项目有利于提升企业产能,优化产品结构,提高盈利能力,增强核心竞争能力。
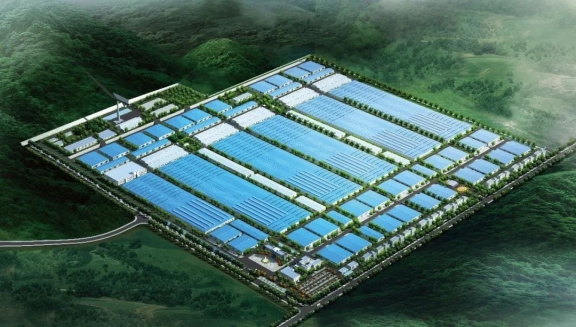
另一个项目,则是贵州轮胎位于越南前江省新福县龙江工业园海外工厂、年产95万条高性能全钢子午线轮胎项目。据中国轮胎商务网了解,该项目投资约11.76亿元,建成达产后,预计可实现年平均收入12.25亿元。就在今年4月,贵州轮胎越南工厂另一项目——年产120 万条智能工厂已实现首胎成功下线,标志着贵州轮胎即将实现国内、国外双基地生产模式,形成国际化、智能化、绿色化高质量发展新格局。

两个项目均以“智能制造”为核心,围绕公司优势主业进行发展。“年产300万套高性能全钢子午线轮胎智能制造”项目全部聚焦于生产全钢子午线轮胎,将通过智能生产设备、智能检测设备和智能物流设备建设,利用大数据、5G连接和工业制造的深度融合,打造基于工业物联网的智能生产线。项目达产后预计产生年销售收入296604.00万元,税前内部收益率为15.42%,具有良好的经济效益。
“智能分拣及转运中心”项目主要通过新建立体智能成品仓,购置智能化仓储设备,扩大全钢子午线轮胎仓储容量,实现仓储立体化、分拣自动化、调度柔性化,从多方面提高公司智能制造水平。项目实施后,将实现每日约16000条成品胎的自动分拣入库及每日约25000条成品胎出库,具备29万条成品胎的储量。
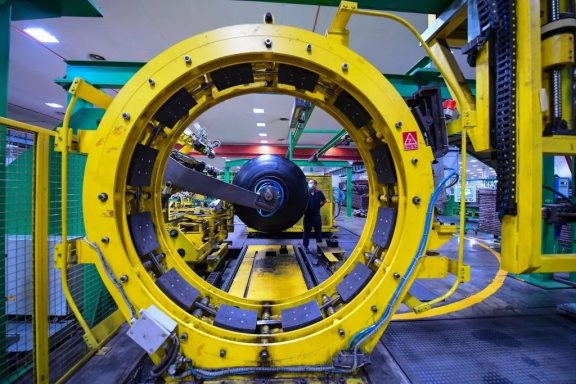
此前,公司借助异地搬迁的有利时机,建成了扎佐一期、二期项目,正在建设扎佐三期项目。目前生产厂区规划科学,生产环节布局合理,在计划、排产、投料、制造执行全流程推行了信息系统,采用多轴机器人、AGV穿梭机器人等多项智能化设备,应用5G专网技术打造了全连接工厂,实现了基于大数据的智能化、数字化的敏捷生产线。此次募投项目实施后与整个厂区配套,是公司智能制造体系 的有效补充,有助于实现智能化转型的战略规划,全面提升产能和管理水平。
贵州轮胎股份有限公司前身为贵州轮胎厂,始建于1958 年,1996 年改制为上市公司,并更名为贵州轮胎股份有限公司,股票在深交所上市交易,简称“贵州轮胎”,证券代码“000589”。是贵阳市规模最大的生产制造型企业,是国家大型一档企业、全国520户重点企业、全国十大轮胎公司和工程机械轮胎配套、出口基地之一和全国化工企业百强之一,已被列入国企改革“双百行动”和贵阳市首批“百亿企业”名单。公司主要从事轮胎研发、生产及销售,主要产品有“前进”、“大力士”、“多力通”、“劲虎”、“金刚”等品牌卡客车轮胎、工程机械轮胎、农业机械轮胎、工业车辆(含实心)轮胎和特种轮胎,规格品种多达3000多个,是全球商用轮胎规格品种较为齐全的轮胎制造企业之一。