炭黑产业网据轮胎报消息,双星集团:绿色轮胎的智能制造。
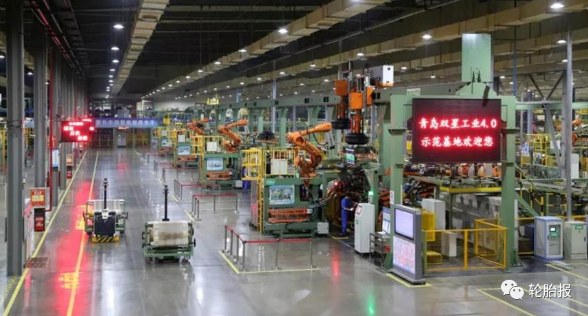
2010年以来,轮胎行业由于受国内市场需求下降、美国双反、橡胶关税等影响,导致大部分企业销量、收入、利润持续下降,减产、停产、破产企业接踵而至。传统产业尤其是轮胎行业,正在推倒重建,谁有竞争力,谁才有可能存活下来。作为传统的劳动密集型、资金密集型、资源密集型、封闭化和同质化严重的行业,双星轮胎的技术、工艺、产品、设备全面落后,导致双星多年在亏损的边缘上徘徊,企业亟需突破限制和现状。2017年开始,双星建立全球第一个全流程的商用车胎工业4.0工厂,打破欧美的技术壁垒,工厂的智能化程度达到世界领先水平。
01应用成效
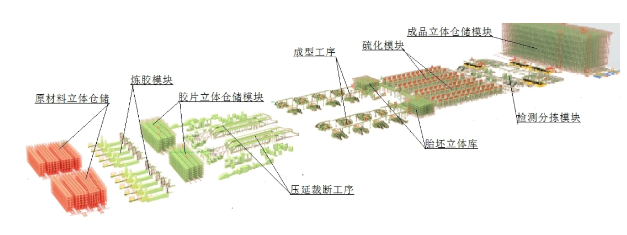
1、应用成效
(1)行业首创轮胎个性化定制订单模式 自2019年推行个性化定制模式以来,定制业务提升45%,定制订单收入从0增长到300万美元。
(2)全流程智能化柔性生产 自2016年开始运行以来,订单响应速度由7天缩短为8小时,人工效率提升3倍,不良率降低80%以上。
(3)数字化的智能生产管控体系 自2016年开始运行以来,问题响应时间缩短99%,OE合格率提升6%,一次合格率提升10%,安全事故降低93.3%,生产效率提高20%以上。
2、示范性和可复制可推广性
(1)通过把握轮胎产业发展大势,抓住“互联网+”和“中国制造2025”的新机遇,创新驱动,自我颠覆,变“新常态”为“新抢态”,积极探索轮胎工业转型发展新模式,在行业内抢先从“汗水型”走向“智慧型”,建成投产全球第一个全流程“工业4.0”轮胎智能化工厂,成为传统轮胎生产企业“两化”深度融合示范。
(2)通过轮胎行业智能制造体系的搭建形成成熟的智能工厂模型,再加入通用技术(包括视觉技术、智能传感器、信息自感知、网络通信技术)、工业物联网、工业云服务模型、工业大数据服务、工业互联网架构等,能够在轮胎行业和其他重点领域快速复制并推广应用。
(3)实现了传纹轮胎行业的智能定制,为行业提供了全新运营模式示范样板。
(4)双星建立的绿色轮胎全流程智能制造样板工厂为行业转型提供服务,4.0工厂的经验已成功复制到湖北十堰工厂,打造华中地区首个工业4.0工厂。目前正在推广筹建青岛星航橡胶科技有限公司,建立的全球轮胎行业第一个“共享”绿色密炼中心,该项目为炼胶行业内第一个工业4.0智能化工厂。
(5)致力于打造汽车后市场第一服务品牌——星猴车政,实施远程监测运维服务——“云犬“TPMS监测系统。实现了由双星轮胎到其他品牌轮胎、再到汽车后市场的其他产品和服务的共享;在行业内具有可复制性和推广性,对推动轮胎行业的可持续发展、行业内企业智能制造的转型升级和智能服务模式探索都起到了标杆和示范作用。
02主要做法
绿色轮胎全流程智能工厂打破了传统轮胎企业的生产工艺和集中式的生产方式,集成信息通信技术、数字控制技术、智能装备技术,实现企业互联化、组织单元化、加工自动化、生产柔性化、制造智能化,搭建了一个覆盖从用户需求、产品设计、研发、智能制造、供应链和汽车后市场智能服务等关键环节的智能生态系统。并在轮胎制造行业及汽车后市场服务行业推广复制应用,实现基于轮胎全生命周期的智能制造、智能服务新模式、新业态。
智能工厂中的设备包括11种智能机器人,80%是双星自主研发和生产,人工效率提高了3倍,产品不良率降低了80%以上,工艺数据自动采集达到98%,自控投用率达到96%。同时,采用了双星独创的MEP智能信息匹配系统,实现物、人、设备、位置的信息智能匹配;工厂全流程实现轮胎智能定制、智能排产、智能送料、智能检测、智能仓储和智能评测。关键技术装备、软件安全可控率92.2%,双星自主设计制造达81.2%。工厂采用的APS智能排产系统,被德国西门子公司专家称为“全球第二家将APS应用到实际生产中的轮胎企业”。绿色轮胎全流程智能工厂的网络建设主要围绕着生产业务系统所需要的计算平台、网络平台、存储平台、数据备份平台及日常管理运营平台等几个方面进行。采用现场总线、以太网、物联网和分布式控制系统等信息技术和控制系统,建立了设施完善成熟的工厂工业通信网络。全局考虑生产业务系统服务要求资源池主要包括物理服务器和虚拟化服务器资源池;围绕服务器资源池网络配套规划设计;存储资源的整合与分配;日常管理和运营管理支撑IT服务可持续发展等。
03特色亮点
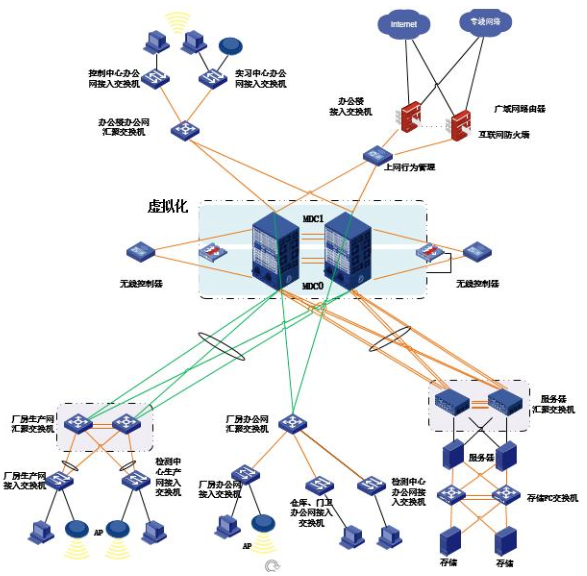
通过搭建智能化工厂信息化系统,集成大数据采集处理技术、AGV智能优化、视觉定位技术、RFID技术等人工智能技术,运用原材料流转卡片、半成品RFID+流转卡片、成品PCR全部RFID、成品TBR RFID+条码的工序介质流转模式,并将MES系统贯穿整个系统,包括整个生产执行过程及所有生产工序机台,在生产计划管理、生产执行调度、工单消耗发送功能、仓库管理功能、设备管理、质量管理、快检管理、能源管理、主数据管理、自动化系统/设备接口、SAP接口、成本控制管理、质量管理等方面进行优化。
具体如下:①利用3D打印技术实现小批量个性化定制。②通过OTO网上下单,PLM全球研发,实现大规模个性化定制。③双星独创的MEP智能信息匹配系统,实现了物、人、设备、位置的信息智能匹配,解决了全球以液体或粉体为原料的制造企业无法全流程实现智能制造的难题。④采用AGV小车、RGV小车、EMS小车、关节机器人、桁架、线体等11种输送设备,实现全流程智能输送。⑤对重量、宽度、厚度等质量指标实时在线检测控制。⑥动平衡、均匀性、X光机等检测设备对接MES实现自动扫码判级检测。⑦炼胶模块:采用串联式密炼机与智能胶片冷却线,挤出与摆片自动抓取、自动取样、自动摆片,下辅机系统自动翻炼。⑧成型模块:关节机器人智能卸胎、称重,桁架机器人智能输送。
以提升本质安全水平为目标,大力实施“机械化换人、自动化减人、智能化无人”科技强安行动,以数字化智能工厂建设赋能安全生产,通过智能工厂建设,近年来,公司安全生产形势持续稳定向好发展,无生产安全事故发生。
1、积极开展设备本质化安全性能改造,对重点设备的上/下料区域、设备运转、传动部位等安装光幕、联动报警等装置,实现了设备误动作、人员误操作、人员不受伤害。
2、通过加大智能设备的投入改造,实现了炼胶、裁断、成型、硫化等生产线智能化生产,车间内配备AGV智能小车,使人员减少一半以上,降低了工作强度,既提升了生产效率又保障了安全。
3、建立安全生产全流程监控监测系统,实施24小时对生产、仓储区域的动态监控,监控中心值班人员一是查看现场正常运营生产状况,二是通过监控抓拍违章并通知到职工本人现场纠正,降低了安全风险。
4、通过双重预防体系、特殊作业报备平台等,实现了检查区域全覆盖、重点作业(风险点)全面受控,线上隐患下发、隐患整改、隐患闭环。
5、建立了协调联动的火灾自动报警系统,实时预警、报警监控,保障能够“救早、灭小、三分钟到场”。
(原标题:数字企业 | 双星集团:绿色轮胎的智能制造)