王象民 编译
炭黑细粉含量属材料合格证中的原材料质量参数。但炭黑生产厂家只能给出供货或出厂前的数值,也就是说,没有也难以考虑车运和风送因素。所以,炭黑细粉含量可能随车运和风送过程的不同而产生明显变化,以前的研究已表明了这一点。同时该研究也表明炭黑颗粒的破坏取决于炭黑结构。
炭黑细粉含量对混炼工艺和胶料性能影响的早期研究是在以EPDM和炭黑N650为基的两种专用橡胶产品配方上进行的。另一个也同时发生变化的原材料参数是所用聚合物长链的支化程度。本文研究了高活性炭黑N234。此外,在风送系统中会产生不同的细粉含量。以此炭黑混入标准的轮胎胎面胶料。假定混炼过程中活性炭黑的行为与半活性及非活性炭黑不同。另外,配方必须具有显著的市场适用性。
1 实验
1·1 配合剂
如前两次研究工作所描述,用同样方法制备了不同细粉含量的炭黑。本研究采用DegussaN234炭黑,所获得的炭黑细粉含量分别为18%,38%和49%。也研究了细粉含量为2%的未输送炭黑。表1为所研究配方。
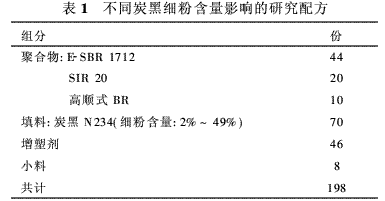
1·2 试验设备
用法雷尔Bridge F70,采取两段法进行混炼实验。该密炼机具有双刀型的切向转子,混炼腔70L。胶料在开炼机上用8mm辊距尽快出片以免过炼。该胎面胶通过热喂挤出机挤出,按生产工艺,在挤出前还进行了一次混炼。用所研究胶料作为胎面胶料制备具有Vredestein Protrac 2si胎面花纹的195/65RI5H轮胎,先在全自动轮胎成型机上成型,然后硫化。
胶料混炼后,再没有其他工艺参数变化。用该胶料制成的轮胎进行试验。对于此类原材料变化来说,轮胎的滚动阻力和磨耗花纹是很重要的。按照Grosch试验方法对后者进行试验,此实验方法模拟实际道路情况好;另外还通过实际道路磨耗进行了评价。按照ECER30方法进行高速行驶试验,这对于批准轮胎工艺是非常重要的。
1·3 混炼过程
如有时轮胎工业中所采用的一样,胶料采用两段混炼法生产。但如果是白炭黑胶料时则为3段或更多。预试验过程中,通过观察上顶栓运动,可以找到最佳填充因子,但不幸的是,所选择的混炼设备不能监控上顶栓位置。因此,先将聚合物(在母料段)捏炼或共混60s,然后加入炭黑、硬脂酸、氧化锌和操作油,在220s后风送清扫,并在进一步返炼后于130℃下料。注意到第2个最大动力消耗峰在风送段后达到,意即将炭黑完全混入胶料中,但是该过程受温度的影响。在终炼阶段,将冷却的胶料塑化45s后加入硫化剂,再混炼125s,然后在73℃下料。混炼试验的目的是运用现有混炼技术在尽可能短的时间里显映出质量参数炭黑细粉含量最大程度的影响。随后,将胶料在开炼机上以8mm辊距,用最短的时间出片,并尽可能少的将能量输入胶料。
2 结果与讨论
图1示出了母炼胶混炼段及终炼胶混炼段动力消耗与混炼时间和细粉含量的关系。如图所示,此类胶料中细粉含量的影响并不明显。
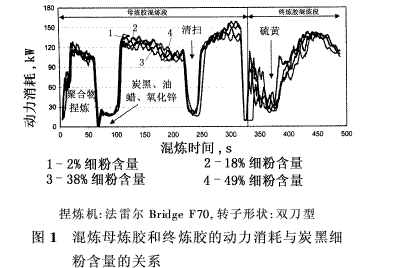
聚合物塑炼后,含有未破裂炭黑的胶料仅可看出稍高的最大动力消耗,在随后的打滑阶段,只能观察到因为高细粉含量引起更强的壁面打滑阶段的略明显的最小动力消耗值。在上顶栓清扫后的混炼段,如同前面观察到的趋势一样,动力消耗达到第2个最高峰,在这以前的研究中也发现过。尽管混炼工艺受温度影响,但是由于过程中细粉含量的影响轻微,胶料温度没什么变化,所以所有胶料差不多在同样时间排料。但是必须考虑到这里用的是双刀型转子,在用更强劲转子甚至互啮合转子时,细粉对工艺的影响就可能更大一些。通常,由于炭黑细粉含量不同导致炭黑混入时发生明显变化在轮胎工业中是人所共知的。在随后的终炼胶段,因母炼胶的吸收行为导致开始时动力消耗波动很大。但在加入硫化剂后,再看不到不同胶料间的明显变化,这可归因于质量参数即细粉含量的变化。另一方面,在混炼过程中,高细粉含量的胶料粘性较差,意即不同的胶料质量,但是此影响仅仅在开炼机初始运转时才观察得到。
因此,有待确定,是否在细粉含量变化最大的母胶混炼过程中,趋势与以前的试验相同。但也不清楚是否本试验的分布情况与前面提到的早期研究例子相同。然而必须再次指出,炭黑细粉含量导致混炼过程的不同与所用转子几何形状有关。对于母胶混炼,本试验所用的双刀型转子,实际中不常用。
混炼结果可以解释为:所用丁苯橡胶(E-SBR1712,50MU)为冷聚充油型,其特点是苯乙烯单元分布稳定和较宽的分子质量分布[Sch1991]。天然橡胶(NR SIR 20,85MU)性能特征也是很宽的分子质量分布,从而工艺性能极好,只有一些长链分支能通过凝胶渗透色谱证实。另一方面,聚丁二烯橡胶(BR,42MU)具有严格的线性链结构。可以假定,E-SBR和NR的长链支化程度远远小于早期研究的高支化的EPDM橡胶。另外,这里的捏炼使链长缩短而不碎化。这意味着与EPDM胶料相比,在捏炼机中会较快地形成均匀且密实的胶料,会消耗更多的动力(见图1)。由于该类填料如炭黑能更好的混入橡胶,尤其是更快,因而细粉的影响相对来说是显著的。这样可以推论,细粉含量对混炼工艺的影响很大程度上也取决于各聚合物的混入性能。但本研究不去证明这一点。
轮胎最重要的性能是所谓的“魔术三角”,即磨耗、滚动阻力和制动性能。当磨耗程度低时,轮胎的使用寿命就长。滚动阻力越小能耗越小。基于安全的原因,制动性能是非常重要的,尤其是在雨雪天气时,这些性能互相依赖似乎也是合乎逻辑的,比如非常高的滚动阻力会改善刹车反应能力,此时传输力较大,反之亦然,但是传输力增大会加大油耗和磨耗。轮胎的另一重要性能是其速度级别。本研究所用的轮胎结构速度可达210km/h。所用胶料配方用于胎面。因为尚不知炭黑细粉含量如何影响这些轮胎的安全性,因而进行了高速试验。
滚动阻力反映了单位距离的能耗,等于实验表面的接触力正切标量总和。图2示出了与细粉含量和速度相关的滚动阻力系数,这是由滚动阻力和车轮压力计算出来的。如图2所示,细粉含量变化时,滚动阻力系数没什么变化。
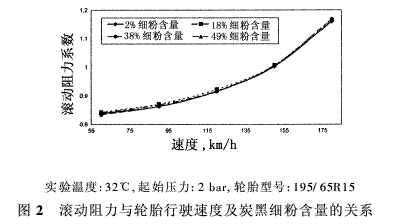
轮胎磨耗受接触面行驶速度和耗散能的影响。通过这些变量可以建立所用胶料和磨损表面的结构性能之间的关系。为得到实际试验结果,必须在可重现路面进行试验,这就会有昂贵的耗费,要么就必须在实验室建立行驶速度和表面结构与道路的类似能量关系。本研究用来测定磨耗的实验室磨耗试验仪100(LAT 100)可以满足此类和更多的要求。图3示出用LAT 100测定的磨耗与速度、耗散能以及细粉含量的关系,此时是针对未破坏炭黑与38%细粉含量和未破坏炭黑与49%细粉含量的两种情况而言,未破坏炭黑作为参照。比如在早期文献中报道的理论关系及其研究,它给出了实验结果与实际道路状况的关联。
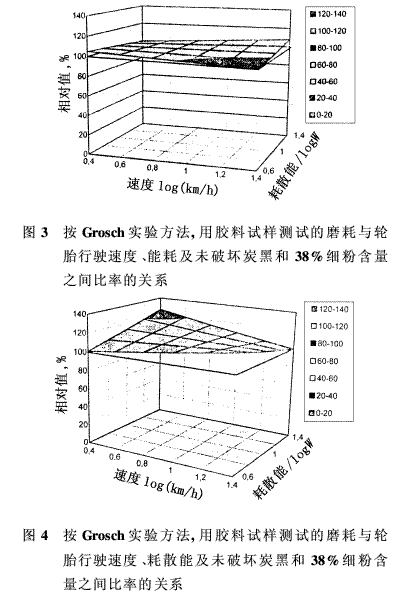
如图3中可以看到的,按分级值来看,当细粉含量由2%(未破坏)增至38%时,耐磨耗性仅有很小的变化,处于该方法的分辨率之内。
高细粉含量时得到的不同的结果清楚地示于图4。图4表明,从轮胎速率和耗散能来说,高细粉含量具有磨耗性能方面的优点。如上述混炼工艺分析中所讨论和早期研究的,炭黑细粉含量对混炼工艺的影响取决于聚合物的混入性能或所并用聚合物的混入性能。但是,聚合物粘度和聚合物支化程度已被公认为混入性能的影响变量。当聚合物粘度和支化程度降低时,炭黑细粉含量的影响也相应减小。如已测定的那样,该并用聚合物显示出良好的混入性能。
因此,可以假定,炭黑聚集体或小球粒碎片混入聚合物基体快。因此,两种作用有利于分散:首先,炭黑被破坏,其次,几乎是立刻混入。这样,就有相对更多的时间用于较小的和部分破坏的炭黑聚集体的分散,这对所要求的分散度有正面的影响。还可以假定,两段工艺会增大该影响,因为在终炼胶混炼阶段初始,会再次对胶料施加很高的剪切力。这在胎面胶进一步挤出前的胶料返炼中也存在这种情况。
如早期研究发现和一般所预计的,炭黑混入过程中所发生的变化随着炭黑分散的变化而终止。尽管由于用老式切向转子观察不到大的工艺变化,母炼胶仍然随细粉含量的变化在开炼机上表现出不同。分散测量是用所谓的RELMA装置在本研究设计方案中进行的,结果如图5所示。
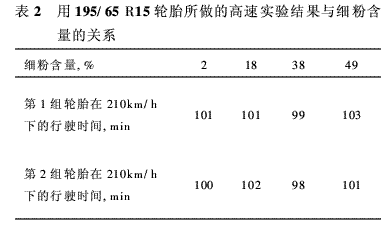
强度比的平均值反映了胶料基体中所分析元素的相对量值,变化系数给出了各自分散的信息。由于元素含量影响变化系数,所以,首先去了解每批胶中是否各元素的量相同是很重要的。分析了终炼胶的硫黄和锌。可以看到,两化学元素的重量值非常精确,锌的分散非常精确(变化系数低表明分散值好)。另一方面,硫黄的分散似乎与细粉含量相关,在早期的研究中也得到相似的结果,虽然这些情况下硫黄是与炭黑一起加入的。这里,硫黄是单独在第2混炼段加入的。结果再次表明,炭黑细粉含量不同,获得的母炼胶质量的确不同,这证实了混炼行为观察的结果。
高速实验也获得了通过,这意味着实际上在各质量参数上没有造成什么差别。在该实验中,轮胎加速到最大速度并保持到破坏,如胎面自己从轮胎上分离出来。这些轮胎的最低要求是210km/h下行驶75min。如表2所示,无论细粉含量大小,轮胎只在大约100min后破坏,破坏图象也是相似的。
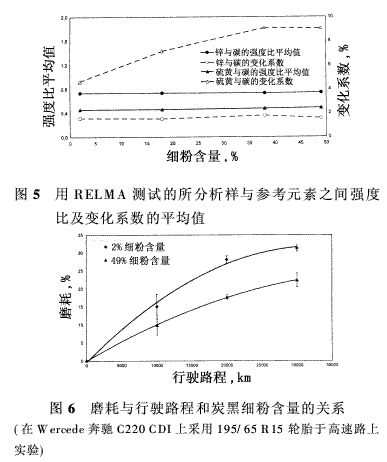
为验证Grosh实验结果,又进行了道路磨耗实验,并且用两组轮胎实验,一组含2%细粉含量的未破坏炭黑,另一组为含49%细粉含量的炭黑。都在几乎恒定的条件下(除了气候变化)用Mercedes奔驰C220 CDI行驶。由于成本的原因,没有雇用特别的驾驶员,但有一著名车手随时准备驾驶驱动轮胎并完成磨耗实验。主要的行驶道路为高速公路,每组轮胎行驶30000km,每10000km测量一次。由于该轮胎胎面配方与通常的略有不同,结合考虑该车型,特殊驾驶许可证由德国在Flensburg的“Kraftfahrt Bundesamt”签发。许可证是按有限时间的实验室实验结果为基础(尤其是高速实验)。磨耗百分数是按每组4个轮胎不同的测量点(每胎宽向的4个固定点)计算的,并算取平均值。进一步假定,轮胎胎面花纹厚度最少必须保持2mm,这样就估算了寿命百分数,由此而计算的磨耗百分数示于图6。
如图6所表明的,的确用49%细粉含量破坏炭黑制成的轮胎似乎有耐磨优势。含未破坏炭黑的轮胎明显磨损较快,Grosch实验也指出了这一点。分析30000km的行驶距离,含破坏炭黑轮胎的磨耗不到10%。可是问题是,是否磨耗随行程线性增加(这是预期的)?是否如图6所示的低于线性增加?如为线性关系时,则含49%细粉含量炭黑的轮胎理论上会有为1.4倍的较长寿命。可以假定,本研究获得的观察结果源于炭黑细粉含量的变化。如早期所研究的,似乎细粉含量增加肯定有利于聚合物的快速混合,但与混入聚合物基体的完整炭黑球粒相比,破坏的炭黑分散程度差一些。
如果观察到完全不同的情况,事实上差别相当大,则就必须考虑上面指出的那样,轮胎不是在绝对相同状况下行驶的。两组轮胎都是在2003年进行行驶实验,但第1组含破坏炭黑的轮胎是在夏天进行实验的,第2组是在8月中旬开始直到11月结束。2003年夏季温度高少雨,而自8月开始下雨气温下降。如果在轮胎行业做此实验,就会每天互换轮胎以尽可能避免条件差别。而且,焦点会放在两组轮胎实验的精确循环平衡上,但在这里是不现实的。
3 结论
本研究采用含高活性炭黑N234的轮胎胎面配方,研究了炭黑质量参数细粉含量对于混炼及某些胶料性能的影响。
研究表明,炭黑细粉含量对混炼工艺没有明显影响,但是可以观察到在混入炭黑段壁面打滑略微增多以及不同的混炼行为。假定由于其线性分子链结构,所用并用聚合物具有如固体的快速混入性能,因此推导出炭黑聚集体小则分散差,这在混炼时间相同时是一个优点。RELMN测试结果证明了母炼胶的质量不同。
观察各自胶料的最终产品性能,可以说,滚动阻力和高速实验结果没有显示出与炭黑细粉含量任何关系,但是,Grosch实验在实验室磨耗条件下给出在最高炭黑细粉含量时变化明显,与轮胎行驶速度和耗散能有关。在道路实际磨耗中在行驶30000km时观察到同样的结果。含最高炭黑细粉含量的轮胎比含最低细粉含量2%轮胎的磨耗小。
这样可以得出结论,炭黑细粉含量对最终产品性能有影响———这里是正面的影响。在早期的研究中,炭黑细粉甚至影响混炼工艺。但是,不能推论出提高炭黑细粉含量就能提高最终产品性能。这种情况下将产生以前文献指出的关于风送系统的工艺大难题,此外通常预计会产生大的工艺问题。但这里目的是证明原材料质量参数会影响工艺性能以及胶料和最终产品性能。回顾所有关于炭黑细粉或其他原材料质量参数方面的研究,完全可以推论,保持该质量参数恒定不变以保证稳定的生产工艺并获得高质量橡胶产品是非常重要的。因此,强烈建议购买高质量原材料以及加工设备以克服此类问题。
参考文献:
1 H.Keuter等,《K.G.K》Vol.58,No.11(2005),581~585