Wilma Dierkes,Jacques W.M等著
朱永康译,瞿光明校(中橡集团炭黑工业研究设计院,四川自贡643000)
最近几年间,开展了许多项目来改进白炭黑技术。其中大部分工作集中于新的偶联剂,特别是硅烷类偶联剂,以及新的白炭黑品种,例如高分散性白炭黑。而对加工设备,如应用于白炭黑胶料的更经济、加工更安全的专用密炼机的调整或研发,则关注较少。
在传统的炭黑混炼设备上混炼白炭黑胶料,是一种常见的习惯做法。由于其要求对温度进行精确的控制,所以最好在啮合型密炼机内混炼,不过也可以使用切向型密炼机。这些设备都是为了进行分散和混合设计的,而不是为白炭黑胶料场合所需的化学反应设计的。因此,白炭黑胶料需要外加几步,来完成白炭黑的硅烷醇基与偶联剂的乙氧基之间的化学反应。这种化学反应,需要130℃以上温度引发反应,但为了具有较高的反应速率,最好在更高的温度下进行。另一方面,硅烷化温度应该远低于焦烧温度。硅烷化这一步往往要达到1 4 5℃左右的温度水平。为了保持在这一较窄的温度范围内,白炭黑胶料需要最高温度约为1 5 0℃的几个混炼步。
白炭黑和硅烷在偶联反应期间生成的乙醇是另一个问题。当所有的乙氧基团发生反应时,胶料中每使用1 g硅烷就会生成大约0.5 g(0.64 ml)乙醇。在加工车料量大的生产型设备上,这将积累数量相当可观的乙醇——它或者重新在混炼室内冷凝,或者蒸发掉。混炼室内的乙醇如果不排除掉,便会造成胶料打滑,从而降低混炼效率。不仅如此,如果车料中的乙醇浓度太高,还会延迟硅烷化反应。
这些与白炭黑胶料加工有关的问题,向来主要是从原材料方面来着手处理的。新研发的白炭黑品种具有高分散性,可缩短分散良好所需要的时间。而分散良好是填料粒子良好硅烷化的先决条件。这些白炭黑品种可以分散至基本粒子的水平。
为了减小混炼及硅烷化期间的焦烧危险,研发出了新型硅烷偶联剂。这些偶联剂中含有少量的硫磺、一硫化物或二硫化物,而不是四硫化物,例如是双-(三乙氧基硅氮烷丙基)二硫化物(即TESPD),而不是双-(三乙氧基硅氮烷丙基)四硫化物(即TESPT),或甚至无硫分散剂。还试验了最常用的硅烷TESPT的其他变种,部分取得了非常好的结果。单-乙氧基硅氮烷丙基硅烷是只靠一个乙氧基与白炭黑偶联的硅烷,它所具有的优点是硅烷化反应期间产生的乙醇量仅相当于TESPT反应所产生乙醇量的1/3,但是其硫化制品的性能却相类似。
开展了一些工作来改进白炭黑胶料的加工,比如,调整混炼工艺或选择现有的最适于白炭黑的密炼机。通过在最终混炼步,而不是在第1混炼步添加氧化锌,能够降低焦烧的危险。就混炼设备而论,最好使用啮合密炼机,因为它至少对温度的控制严密,允许其接近焦烧温度进行工作。密炼机串联工作使其获得进一步的改善。第1台普通密炼机在标准混炼条件下运行,用于混炼和分散。第2台密炼机则专门为硅烷化反应而设计。
1硅烷化反应
在硅烷化反应期间,白炭黑填料表面的亲水特性发生变化而更具疏水性,而提高这类填料与聚合物的相溶性。偶联剂(硅烷类)与白炭黑表面的极性硅烷醇基反应,在外面围绕填料粒子与碳原子和硫原子形成一层外壳。这一主反应在130℃左右开始。
标准的偶联剂当推双官能团硅烷,其中最常用的为双-(三乙氧基硅氮烷丙基)四硫化物(TESPT)。偶联剂和填料表面硅烷醇基之间的第1步反应示于图1。
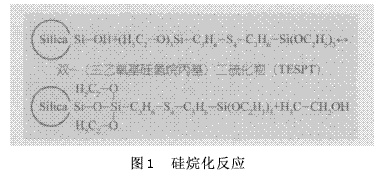
在硅烷化反应的第2步,偶联剂的其余乙氧基与邻近的乙氧基或硅烷醇基反应。填料粒子和偶联剂之间的这种化学反应是平衡反应。因而,为了获得良好的硅烷化效果,排除硅烷醇至关重要。普通偶联剂所含的硫磺,为硫化期间构建填料-聚合物网络必不可少,它可赋予白炭黑胶料特殊的性能曲线。与此同时,它也是硅烷化反应的限制因素;加工时温度范围的上限,就是由焦烧危险性规定的。因此,硅烷化反应的温度范围被限制在130~150℃之间,具体取决于偶联剂和白炭黑的种类、混炼过程及混炼设备的类型。
2 Payne效应
P a y n e效应常用来对橡胶胶料中的填料-填料相互作用进行量化,后者则与硅烷化赋予白炭黑的疏水性成反比。
它与储能模量G′成正比。下列效应为促成储能模量的因素:
(1)由Guth、Gold和Smallwood公式描述的填料粒子在聚合物基质内的流体动力效应;
(2)连接聚合物链的交联网络;
(3)橡胶和填料之间的化学相互作用与物理相互作用;
(4)填料-填料相互作用。
只有填料-填料相互作用在小应变级别内才具有应变依赖性。填料网络随着应变的增加而逐渐被破坏;绝对应变值比破坏聚合物-聚合物网络所需的应变值要小,远远低于10 0%。这种储能模量随应变增加而减小的现象,就称之为“Payne效应”。在本研究中,为了对硅烷化反应进行评估,取用了应变由0.5 6%增加到1 0 0%而储能模量减小的特点,来排除填料和聚合物基质之间的远程力。
3实验
为了研究密炼机变量和硅烷化效率之间的关系,制备了车料量很大的一车母炼胶,然后在不同的实验室密炼机和生产型密炼机(表1)上,进一步作各种条件下的母炼胶的混炼实验。
3.1母炼胶的制备
所有研究,均采用基于S-SBR和BR并用胶(含83.5份白炭黑,以硅烷TESPT或TESPD为偶联剂)的乘用车轮胎胎面母炼胶。该胶料在320 L的啮合密炼机内进行混炼和预分散,混炼步的指纹图示于图2。母炼胶排胶前约60 s达到硅烷化的起始温度130℃;在此期间,硅烷化反应所达到的程度非常有限。
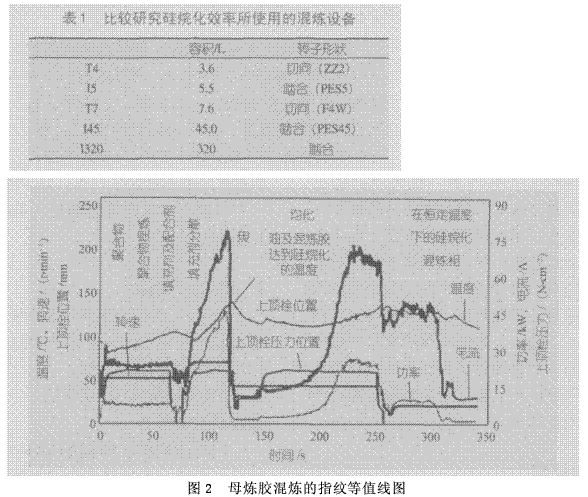
3.2混炼设备
用5种不同的密炼机(如表1所示)来研究硅烷化这一步。本研究采用3种带标准转子的不同规格的啮合密炼机(I5:5.5 L;I45:45.0 L;I320:320.0 L;I表示啮合)。另外,还使用了2种规格相同但带不同构形转子的切向型密炼机。与带ZZ2-构形(T4)的切向转子相比,带全四棱构形的切向转子(F4W;F7)的凸棱较大而角度较小,这使得径向混炼和分散方面的效率较高。
所有实验均使用早些时候制备的预分散母炼胶。随着上顶栓的闭合,在密炼机内使该母炼胶尽早达到最终硅烷化温度。在达到硅烷化温度后,通过调节硅烷化反应期间的转子速度,来保持这一温度水平。
3.3试样制备和分析
完成硅烷化这一步后直接测定胶料的门尼黏度,就可以确定硅烷化的程度。这些数值初步表明了填料的分散度和硅烷化程度。而硅烷化反应的更准确的结果,则要通过测定P a y n e效应来获得。这2项测定的决定性差别,在于进行测定时所选择的应变:Payne效应只在低应变值下测定,而测定黏度则采用较高的应变。在混炼及测试期间对试样进行冷却,以免填料发生再次附聚。胶料的制备和分析,采用以下设备和条件:
(1)胶料温度——车料排胶后马上用热电偶在密炼机外测定;
(2)黏度ML(1+4),100℃——2000E型门尼黏度计;
(3)Payne效应(小应变时的G′)——RPA2000型橡胶加工分析仪(应变扫描:0.56%~100%,温度:100℃,频率:0.5 Hz);
(4)蒸发出的乙醇——乙醇吸附在活性炭上,用气相色谱术进行解吸和定量测定;
(5)胶料的水分——Karl-Fischer电量滴定法。
3.4考察的因素
考察了影响硅烷化效率的下列预计因素:
(1)常压混炼——硅烷化这一步在常压即密炼机上顶栓抬起不加压的情况下进行。为了改善进料性能、硅烷化效率和密炼机能力,对填充系数进行了优化;
(2)不同的密炼机和转子类型——从进料性能、硅烷化效率和焦烧危险性等方面,对转子构形和能力不同的密炼机进行了比较;
(3)在开炼机上硅烷化——预计在开炼机上硅烷化效率很高,因为其乙醇排除效果良好;
(4)空气注入——非常强的空气流吹过混炼室,以排除乙醇;
(5)密炼机温度——考察了混炼室温度设定的影响。
4结果
4.1常压混炼
影响硅烷化反应的因素之一是胶料及密炼机内的乙醇浓度。由于硅烷化属于平衡反应,预计降低胶料中乙醇浓度可提高反应速率。而要达到降低乙醇浓度这一目标,其手段是让硅烷化这一步在密炼机内以常压模式进行。在这一系列实验中,正如实验这一节所述,预分散母炼胶在密炼机内被加热至最终硅烷化温度。一旦胶料达到硅烷化温度(145℃),上顶栓便抬升起来,硅烷化即在密炼机内常压进行150 s。通过调节转子的速度,使硅烷化期间的温度保持在145℃不变。在进行150 s的硅烷化后,让胶料排出常压模式密炼机,作进一步的分析。图3、图4所示的是与常压模式(密炼机上顶栓抬起不加压)相比较,不同密炼机和不同填充系数在标准条件(密炼机)下硅烷化效率的结果。硅烷化效率通过黏度和Pa y ne效应来度量(分别示于图3、图4)。
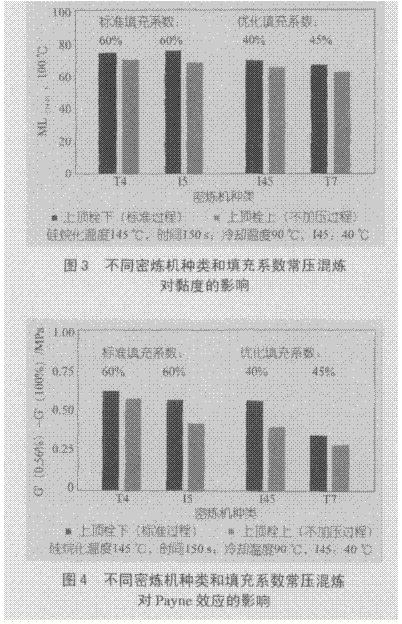
发现白炭黑胶料在标准加工条件下填充系数为典型值(60%),以及为优化的低填充系数(40%、45%)时,硅烷化在密炼机内以常压模式进行,硅烷化效率都有了极大提高。在啮合型密炼机中,这一效果比在切向型密炼机中更为明显。在小型设备(T4、I5、T7)上所发现的结果,在大型的45 L啮合型密炼机(I45)上得到了验证。在I45密炼机中,常压模式硅烷化效率的提高,比起较小型号的密炼机来更为明显。硅烷化的绝对水平与密炼机的规格大小无关。
为改善进料性能因而减小填充系数,对硅烷化效率具有外加的积极影响。把常压硅烷化和减小填充系数这2项措施结合起来,可达P a y n e效应和黏度的进一步降低。采用带F 4 W-转子形状(T7)及减小填充系数的常压模式切向密炼机,找到了储能模量的最低值。
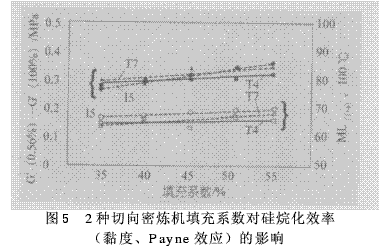
图5所示的是3种不同转子形状的密炼机及其填充系数减小对硅烷化效率的影响,其中2种为带Z Z 2-构形(T 4)和F 4 W-构形(T 7)的切向转子,一种为带PES5构形(I5)的啮合转子。正如Pa y n e效应中可看到的那样,硅烷化效率随着填充系数的减小而略有增加(图5)。这种效应在啮合型密炼机(I 5)上最强,而带ZZ2-构形(T4)的切向密炼机所受填充系数的影响仅属轻微而已。就黏度和Pa y ne效应而言,所有密炼机的硅烷化水平都不相上下。另一方面,能耗则表明了2种密炼机所存在的巨大差异。图6表明,带F4W-构形(T7)的切向型密炼机的能量输入率最低,而其余2种类型的密炼机能量吸收率更高,两者都处于同一水平上。对于F4W-密炼机(T7),保持硅烷化温度水平所需的转子速度完全取决于填充系数,而切向Z Z 2-密炼机仅需直接调节一下温度即可。
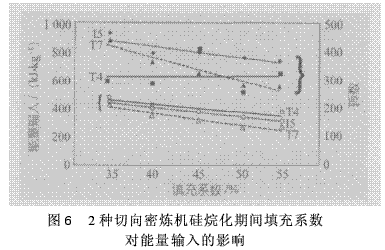
对3种不同的密炼机型号(T7、T4、I5)进行了比较研究。图7a~c所示的是在完全硅烷化过程中,切向F4W-密炼机(T7)在研究的所有温度水平(135~155℃)下给出了最佳结果;在类似的操作条件下,该类转子的黏度及P a y n e效应最低。尤其是在硅烷化的初期(温度水平低,硅烷化时期短),这种密炼机的运行效果要好得多。啮合型密炼机在2种切向型密炼机之间处于居中位置。当硅烷化反应继续进行时(硅烷化时间更长,硅烷化温度更高),3种密炼机之间Pa y n e效应的差异逐渐缩小。与此类似,黏度减小了,但不同密炼机的值并未会聚于一点。
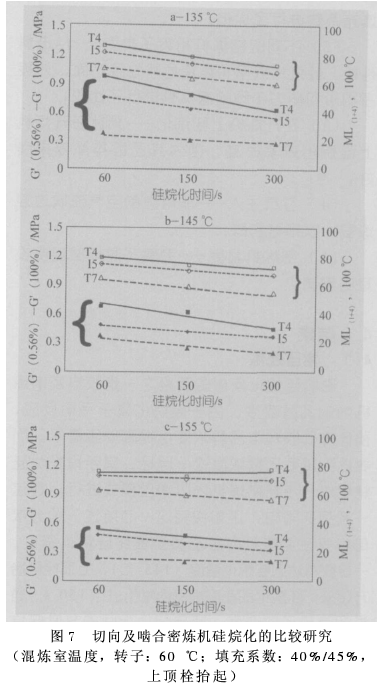
图8a给出的能量输入率表明,啮合型密炼机(I5)吸收的能量比2种切向型密炼机更多。将这2种切向型密炼机加以比较时,带F4W-构形(T7)的密炼机吸收的能量略低于带ZZ2-构形(T4)的切向型密炼机。就总的旋转转数而言(图8b),啮合型密炼机(I5)处于中间地位;可达到一定的温度曲线,带ZZ2-构形(T4)的切向型密炼机需要的转数最高,而带F4 W-构形(T 7)的切向型密炼机需要的转数最低。

4.2在开炼机上硅烷化
预计所用开炼机是使发生硅烷反应期间产生的乙醇蒸发的最有效的方法。让预分散胶料先在密炼机内升至硅烷化温度,再移至开炼机上进行硅烷化这一步。作为比较,将同一批胶料的不同部分投入密炼机,以常压模式在该密炼机内加热并进行硅烷化。图9所示的是,与密炼机内的硅烷化相对照,在开炼机上硅烷化期间Payne效应和黏度减小的情形。未发现密炼机和开炼机之间Payne效应有什么差异,这表明在这些条件下2种情况的硅烷化效率相同。只是密炼机在硅烷化20 min期间其黏度降低更快。
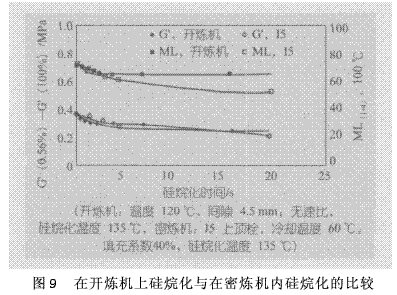
4.3空气注入
提高乙醇排除率的另一项措施是在硅烷化这一步时向密炼机注入空气。首先在实验室内以较大规格设备(I45)进行了一系列试验。空气从密炼机底部注入,没有考虑专门注入空气的出口。在标准条件下将胶料加热至硅烷化温度(145℃)。当胶料达到这一温度后,即开始注入空气,并对转子速度进行调节,以便保持硅烷化所需要的温度。图10示出该胶料的性能以及与相同条件下(除切断空气注入外)硅烷化胶料性能的比较。空气注入降低了Pa y n e效应、黏度及胶料内的水分含量,乙醇排除更为有效。这些结果得到了生产型设备中320 L密炼机内混炼的一系列胶料的验证。注入空气时硅烷化的效率也明显高得多(图11)。所有的其他性能与标准白炭黑胶料的性能差不多。
4.4密炼机温度
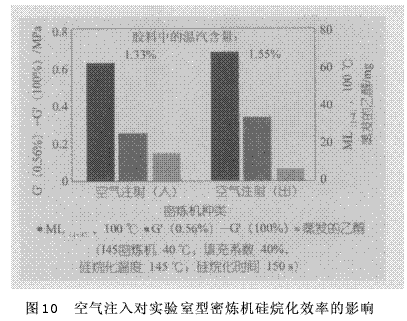
获得良好的胶料冷却效率的一个方法,是降低混炼室和转子的冷却温度。图12a、12b所示的是切向型密炼机(图12a)和啮合型密炼机图12b)中这一措施的影响。在这2种情况下,冷却温度从120℃下降到60℃时,黏度及储存模量均下降。与此同时,保持此温度水平的机械能输入和旋转总转数增加。在切向型密炼机中,这种影响比在啮合型密炼机中更强。
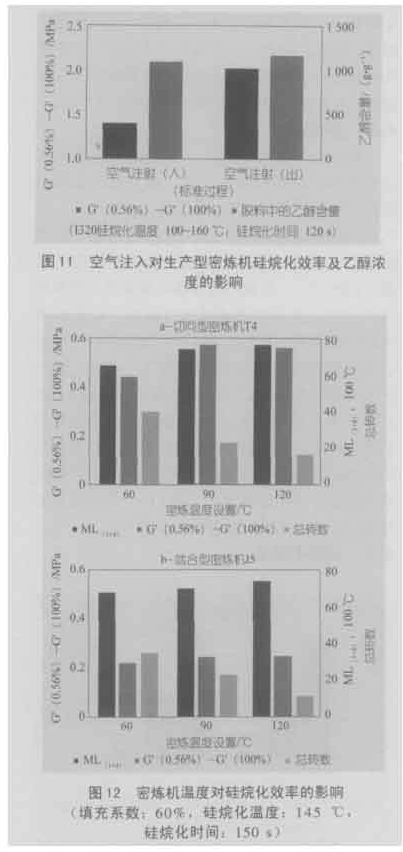
5讨论与结论
5.1常压混炼
胶料内吸收的高浓度乙醇会限制硅烷化的效率。解决这个问题的措施是提高乙醇的排除率,从而促进硅烷化反应。在本研究中,常压硅烷化这一步的确使得乙醇排除率大为提高,进而导致更低的Payne效应和黏度(图3、4)。以这样的模式,乙醇就能够通过料斗口蒸发,使密炼机内因胶料连续再吸收的冷凝乙醇得以减少。如以标准填充系数在常压密炼机中进行硅烷化时,进料性能很不正常,结果是胶料被推入料斗停留,在料斗内经转子处转几转之后,才被拉入混炼室。进料性能可通过减小填充系数来改善。发现啮合型密炼机填充系数40%时,切向型密炼机填充系数4 5%时,是良好的进料性能为一方与密炼机能力降低为另一方,两者之间的最佳折中方案。
填充系数会影响硅烷化的效率(图5)。填充系数越小,混炼室内产生的乙醇总量越少,能蒸发而进入混炼室内的乙醇的自由体积越大。另外,也因填充系数较低,部分胶料通过转子和内壁之间间隙的频率也较高。胶料薄通出片可达更高的程度,胶料蒸发出的乙醇量也增加。由于与切向型密炼机相比其进料性能更不正常,填充系数对储能模量的影响在啮合密炼机中更加明显。因此,通过调节填充系数和改善进料性能所获得的好处,对啮合型密炼机来说更大。在3种密炼机构形之间,未发现Payne效应和黏度水平有重大的差别,但是能量输入率的趋势变化则相当大(图6)。对于带ZZ2-构形(T4)的切向型密炼机,能量输入只受填充系数轻微影响,其结果是旋转的绝对转数随着填充系数的提高仅略有降低。对带F4 W-构形的切向型密炼机(T7),发现了另一种极端的现象:硅烷化期间的总转数及能量输入,两者均随着填充系数的提高而急剧减小。这种密炼机的能量吸收的总水平最低。在该系列的密炼机中,带F4 W-转子的密炼机的效率最高;散失到混炼室的能量少,剪切力高。
对3种类型密炼机(切向:ZZ2,F4W;啮合:PES5)加以比较可发现,带F4W-切向转子构形的密炼机性能最佳,即使能量吸收和总转数较低也是如此(图7,图8 a、b)。这就证明了F4 W-转子在分散和产生新鲜表面方面非常有效。当操作不用上顶栓时,带PES5-构形的啮合转子是效率最低的一种,尽管高能量输入和高转数可达致更新鲜表面的形成。其原因可能是这种密炼机的进料性能太不正常所致。P a y n e效应的差异随着硅烷化程度的提高而缩小,而黏度的差异在整个硅烷化过程中则保持不变。这是2种过程的结果:一方面,黏度因硅烷化程度的提高而减小;另一方面,塑化效率随着温度的增加和黏度的减小而降低。
5.2在开炼机上硅烷化
预计开炼机的硅烷化效率会非常高,然而实验表明实际并非一定如此(图9)。在此实验中,硅烷化是在辊隙4.5 mm的开炼机上进行的。在密炼机中,转子与混炼室室壁之间的间隙是3.3 mm。结果,开炼机上车料薄通出片较厚,因而限制乙醇从胶料中蒸发出来。硅烷化效率降低的另一因素是开炼机上的材料积存。开炼机上某些部分材料通过缝隙,不如密炼机内胶料那么频繁。这2个因素均会限制开炼机上硅烷化的效率。在优化的条件下,开炼机上胶料少些而出片薄些,可进一步提高开炼机上硅烷化的效率。
5.3空气注入
提高硅烷化效率的一个非常有效的方法,是强空气流通过混炼室(图10、11)。注入的空气将乙醇“拖带”出混炼室,从而加速乙醇自胶料内往外蒸发,避免其在混炼室内冷凝成酒精。胶料内乙醇浓度以此方式降低使硅烷化反应的平衡转移到产物一侧,可提高硅烷化程度。另一个因素是空气流的冷却效应,它使得混炼必须要以更高的转子速度进行,以保持这一温度水平。这使得混炼更好且产生更新鲜的表面。这是一个非常有效的措施,很容易在现有的密炼机上实施。
5.4密炼机温度控制
密炼机温度是影响硅烷化效率的决定性因素。更为有效的冷却,例如通过降低混炼室壁的冷却温度,使机械能输入更高。这会促使更新鲜表面的形成,促进乙醇的蒸发。Payne效应为这种作用提供了证据;然而黏度也受到在机械能输入使用下被解聚的影响(图12a、b)。
6总结
在这篇实用研究报告中,实验室以不同的规模并在生产型设备上试验了不同的密炼机和密炼机调整对硅烷化过程效率的影响。发现以下因素可以提高硅烷化效率:
(1)密炼机常压混炼。在混合和分散步后,可以密炼机常压模式进行随后的硅烷化步。这增强了乙醇的蒸发,从而提高了硅烷化的效率。达到这一目标的最佳途径是用2台密炼机协同工作:一台标准密炼机(最好用啮合转子构形)用于混合和分散,随即在一台专门设计的反应器内进行硅烷化反应。硅烷化反应器应能使温度保持在理想的水平,并让胶料中的乙醇蒸发和排出反应室。
(2)转子设计。如以常压模式工作,切向转子在进料性能方面表现更佳,而啮合型密炼机则有温度控制更好的优点。F4 W-转子是一种进取型切向转子,它具有的凸棱比切向ZZ2-转子构形的更大,角度也更小,结果证明它是本研究中硅烷化效率最高的转子。
(3)空气注入对硅烷化效率具有积极的作用,但是不会影响胶料的整体性能。
(4)对冷凝敏感部件(如上顶栓)加热,而对其余的部件进行强化冷却,可以提高硅烷化的效率。
参考文献:
[1]D.Berkemeier,W Haeder and M.Rinker,RubberWorld,34(J uly 2001).
[2]L.A.E.M.Reuvekamp,thesis,University Twente,IS BN 90365 1856 3(February 2003).
[3]P G.Joshi,R.W.Cruse,R.J.Pickwell,K.J.Weller,M.H.Hofstetter,E.R.Pohl,M.E S tout and F D.Osterholtz,Crompton Corp.literature.
[4]J.W.ten Brinke,PJ.van Swaaij,L.A.E.M.Reuvekampand J.W.M.N oordermeer,paper I31A,ACS RubberDivis ion M eeting,October 2001.
[5]T.Früh,L.Steger and L.Heiligef,proceedings of theKautschuk Herbstkolloquium 2002,Hanover,German3y,175(October/N ovember 2002).
[6]L.A.E.M.Reuvekamp,S.C.Debnath,J.W.ten Brinke,PJ.van Swaaij and J.W.M.Noordermeer,paper 112,ACS Rubber Division M eeting,October 2002.
[7]J.Peter and H.Sandau(to Continental AG),Germanpatent D E 199 13 047A 1(23.3.1999).
[8]H.-D.Luginsland,Degussa-Hüls AG,paper presentedat the llth S RC Meeting,Puchov(M ay 1999).
[9]L.A.E.M.Reuvekamp,J.W.ten Brinke,P.J.vanSw aaij and J.W.M.N oordermeer,University Twente,paper at the Kautschuk Herbs tkolloquium,October2000.
[10]A.R.Payne,Rubber Chem.Technol.,39,365(1966).
[11]A.R.Payne and R.E.Whittaker,Rubber Chem.Technol.44,440(1971).
[12]E.Guth and O.Gold,Phys.Rev.,53,322(1938).
[13]H.M.Smallwood,J.Appl.Phys.,15,758(1944).
[14]W.Niedermeier,J.Fr?hlich and H.-D.Luginsland,Kauts chuk G ummi Kunstoffe 55,7~8(2002).
[15]C.Lin et aL,Bridgestone/Firestone Research Inc.,paperno.90,ACS Rubber Division Meeting,October 2001.