王进文 (西北橡胶塑料研究设计院,陕西咸阳712023) 编译
0 前言
胶料混炼是橡胶制品生产过程中的第一步,也是最重要的一步。传统的做法是用大规格密炼机对胶料进行混炼。密炼机中有混炼室和2个转子。在过去的90年里,密炼机混炼技术几乎未发生大的变革。自从1914年用密炼机混炼橡胶获得专利以来,对混炼技术的改进主要集中在转子结构或转子间距的变化上。用密炼机进行间歇式混炼时,按照特定的胶料配方和加料顺序,将各种组分投入密炼机中。该工艺的优点是在胶料配方和加料顺序发生变化时其灵活性很大。不连续混炼的缺点是各批次混炼胶间的质量参差不齐,我们知道的所谓“第一批效应”就是一个例子。密炼机刚起动时混炼室的温度不高,致使头一批胶料的混炼质量较差。因此,常常要将第一批至第四批胶料报废。不连续混炼的另一个缺点是,由于在密炼机混炼过程中胶料温度升高,所以交联剂要在另一个混炼步骤中加入,因而大大增加了成本。采用连续混炼就可将胶料组分稳定地计量加入,且工艺条件恒定不变,因此,可消除胶料批次间的质量差异。连续混炼可用多螺杆挤出机完成,如双螺杆挤出机、行星式螺杆挤出机或环形挤出机。由于多螺杆挤出机的冷却能力极强,因此对各个加工单元的温度可以加以控制。该工艺的其他优点是节能、工艺控制简便,并且,由于减少了粉尘、废气和反应产物的排放量,从而降低了对环境的污染程度。在具备所有这些优点的同时,填料分散和拉伸强度等胶料质量和产品性能也高于或相当于不连续混炼的胶料。
自从白炭黑填充胶料问世以来,这种胶料就成了制造具有低滚动阻力、良好路面防滑性和冬季行驶特性的轿车轮胎的胶料。该胶料的主要原材料是溶聚丁苯橡胶(L-SBR)、顺丁橡胶(BR)、高活性白炭黑和作为偶联剂的双官能有机硅烷(如Si-69)。由于白炭黑表面上有硅醇基团存在,粒子间的相互作用很强,而且白炭黑和橡胶之间并不相容,所以在胶料中加入了硅烷。硅烷能与白炭黑反应,从而改善了填料的分散性能,使不相容的白炭黑相和橡胶相由共价键连结在一起。白炭黑填充胶料一般采用密炼机至少分三步进行混炼,这是一种高能耗、高成本的工艺。密炼机起化学反应器的作用,反应在140°C~150°C的温度范围内进行,混炼时间3 min~4 min。为了保证达到所需的温度,基础胶料的混炼要分两步进行。在反应过程中会产生乙醇。交联剂在第三步混炼时才可加入,最高温度不能超过120°C。
在固定特异公司的专利[1]中描述了白炭黑填充胶料的连续混炼方法,其中提出了用单螺杆和双螺杆及其组合形式连续混炼的概念。Pirell(皮列里)发明的胶料连续混炼系统(CCM)也可用于白炭黑填充胶料的连续生产。由于混炼时所需的反应时间较长,不同阶段需采用不同的加工温度,所以Pirell的连续混炼系统由两台双螺杆挤出机和一个过渡贮料仓组成。第一台挤出机的工作温度范围为150°C~200°C,在该挤出机中完成反应过程。混炼好的基础胶料造粒后暂时存放在过渡贮料仓中。交联剂在第二台挤出机上加入,其最高加工温度为120°C。在固特异和Pirell所描述的连续生产工艺中,所用的原材料都是颗粒橡胶和散粒状白炭黑。
1 行星式螺杆挤出机
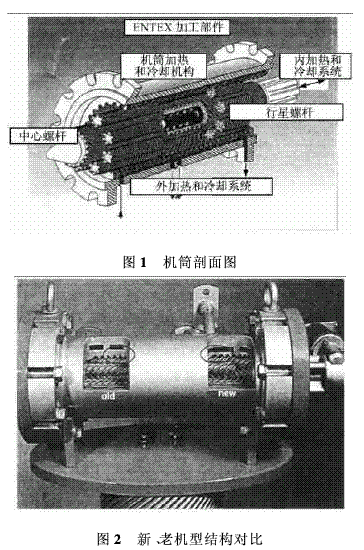
行星式螺杆挤出机现在主要用于涂料、热塑性塑料及化工产品的混合,用于医药和食品行业。行星式螺杆挤出机(图1)的加工部分主要由中心旋转螺杆、机筒和沿圆周分布的行星式螺杆组成。中心旋转螺杆和机筒的温度可以控制,在温度可控的加料段加入计量好的原材料。由中心旋转螺杆驱动,并将扭矩依次分配给行星式螺杆。行星式螺杆沿带有45°螺纹的机筒滚动。由于行星系统采用的是螺旋啮合方式,胶料可以向外旋出,并在旋转部分的出口处同时排料,这样就确保了混炼挤出机具有最佳的自清洁功能。如果采用开放式停止环,除少量残余胶料外,几乎所有胶料都从旋转部分旋出,这能带来诸多便利,例如,可以方便地更换不同颜色的胶料。由于机筒和中心螺杆机构的壁极薄(图2),所以对接触面上的温度可以进行精确控制。再加上高压水加热,并改进了冷却通道的结构,能精确地控制温度,从而对热传递产生决定性的影响。因此,该系统愈来愈受到人们的认可。
机筒采用的是模块结构,几个机筒用法兰连接在一起。中心螺杆延伸至整个加工长度,每个模块可以配置不同数量的行星螺杆。通过中层挡胶环将各个机筒段连接在一起。行星螺杆沿这些挡胶环旋转。通过改变行星螺杆的配置和挡胶环直径,就可以调节胶料熔体的留驻时间和升压。如图3所示,行星螺杆可具有不同的螺纹结构。可以相对于中心螺杆的沟槽或分散环的直径调节自由截面面积(图4)。
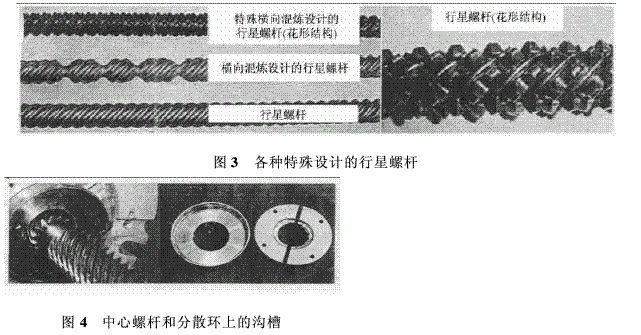
2 研究目的
该项研究的目的是以粒状橡胶/填料复合胶料(RFC)为原料,开发和优化由行星式螺杆挤出机连续混炼白炭黑填充胶料的工艺。所用的橡胶/填料复合胶料(RFC)是一种实验产品,RFC中含有完全硅烷化的炭黑。研究表明,采用冷却效率极高的行星式螺杆挤出机混炼时,可将交联剂直接加入挤出机中,所以,混炼可以一步连续完成。混炼过程中未超过最高胶料温度(120°C)。对胶料性能、硫化胶性能及能耗进行的比较表明,连续混炼工艺具有极大的潜力。
3 材料及加工条件
采用两种E-SBR/白炭黑/硅烷RFC。RFC中还含有4份锌皂作为混炼过程中的加工助剂。锌皂能降低胶料的门尼粘度。RFC粒子的粒径范围为0.5 mm~1.5 mm(图5)。RFC的组成及研究用的胶料配方分别示于表1和表2。
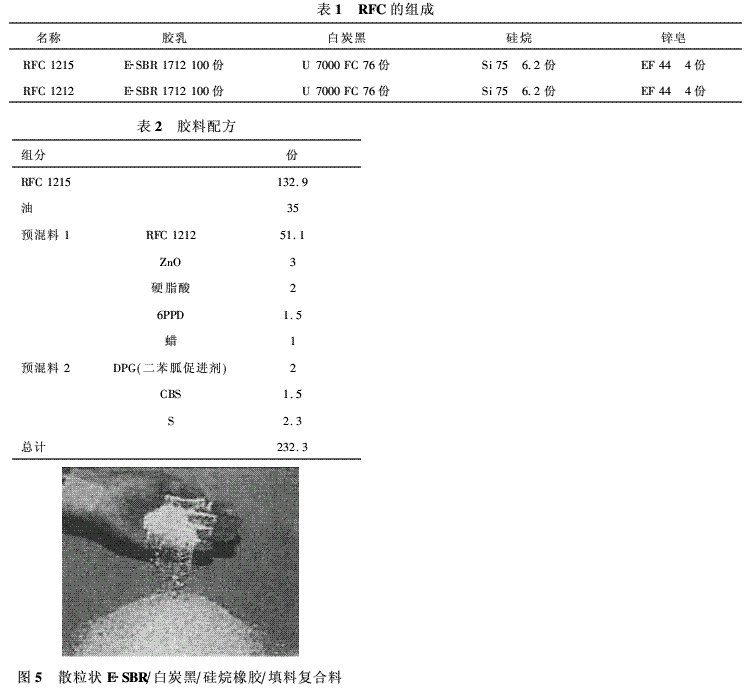
RFC对比胶料在带有啮合转子的1.5 L实室密炼机中混炼,加料顺序见表3。
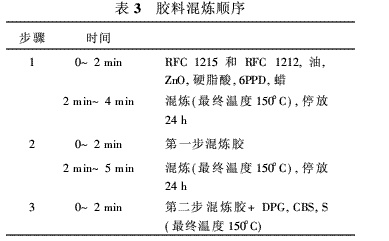
行星式螺杆挤出机(Entex Rust& Mitschke)的参数及行星螺杆的配置见表4和表5。图6示出了加工工艺框图。
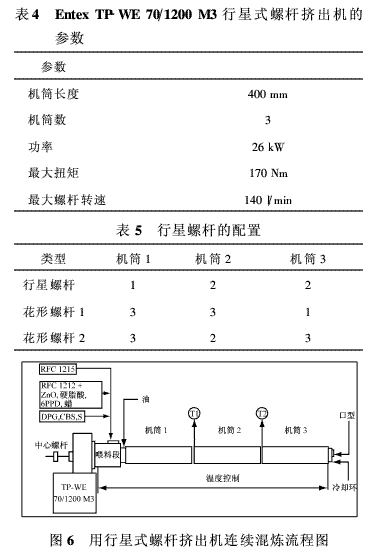
通过重力计量系统将RFC和其他组分,包括活化剂、防老剂、抗臭氧剂以及交联剂加入到行星式螺杆挤出机中。为了减少计量设备,将胶料组分制成了预混料。预混料1由RFC1212、ZnO、硬脂酸、6PPD和蜡组成。交联剂DPG、CBS和S制成预混料2。将软化油加热到60°C,之后注入介于喂料段和第1个机筒之间的螺杆机筒部分。
4 表征
将混炼好的胶料置于双辊开炼机上制成4 mm厚的胶片,于165°C下在电热平板上硫化成2 mm和6 mm厚的试片。生胶性能(门尼粘度)及化胶性能(如拉伸强度)用标准方法测试。用顶部照明显微分散指数分析系统(DIAS)分析填料的分散状况。
5 结果与讨论
由密炼机混炼的胶料参数见表6,由表6数据可见,单位能耗较高。
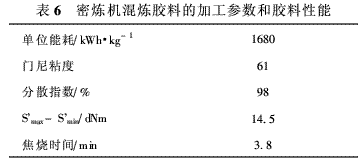
在胶料的连续生产过程中,交联剂通常在胶料挤出前不久加入,与用密炼机不连续混炼时的方法差不多。在本研究中,交联剂及其他所有组分都在喂料段加入。
图7示出了挤出机在填充程度恒定的情况下单位能耗和门尼粘度随产量的变化情况。由图可见,随挤出量的增加,单位能耗下降,门尼粘度升高。这是因为挤出量增加后,为了将15 kg/h产量的恒定填充度70 L/min调高到140 L/min,可提高旋转速度。旋转速度提高,胶料的温度上升,从而降低了胶料粘度和剪切应力。图8示出了各段机筒处的可调节胶料温度以及出口处胶料温度随产量的变化情况。当产量为15 kg/h时,测得的出口处的恒定温度为75°C。如果挤出量提高,胶料温度会线性升高。在机筒1和机筒2处测得的温度相同。在机筒3的出口处测得的温度较低。当挤出量为40kg/h时,胶料温度达到最高许可温度(120°C)。
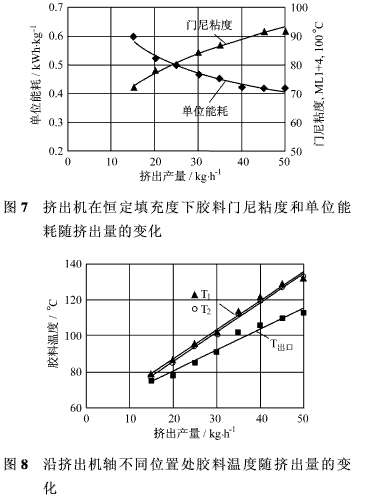
表7中列出了采用间歇式和连续式方法混炼的白炭黑填充胶料的能耗、交联密度(S’max-S’min)及硫化胶性能(如拉伸强度、拉断伸长率和硬度)的比较。与间歇式混炼方法相比,用行星式螺杆挤出机连续混炼能耗降低65%,混炼制得的胶料经硫化后的性能,如拉伸强度和硬度与间歇法的相同。挤出量仅对填料分散和焦烧时间有轻微影响(图9)。连续混炼胶料的性能值与间歇法混炼胶料的相当。在整个挤出量范围内焦烧时间和交联密度(S’max-S’min)都没有变化,这证明在喂料段将交联剂与其他组分一同加入是可行的,这是因为行星螺杆挤出机具有很强的冷却能力。
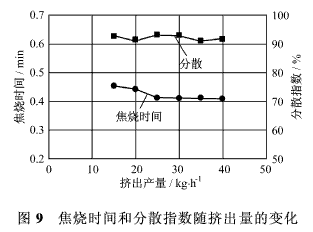
6 结论[2]
以粒状橡胶/填料复合胶料(RFC)为原料,研究了用行星式螺杆挤出机连续混炼白炭黑填充胶料。用一段混炼法混炼了白炭黑填充胶料(所用RFC为E-SBR/白炭黑/硅烷)。由于行星式螺杆挤出机具有较强的冷却能力,所以可将交联剂在喂料段同其他胶料组分一同加入。胶料无焦烧迹象。胶料性能,如填料分散和交联密度(S’max-S’min),硫化胶性能,如拉伸强度和硬度都与用密炼机混炼的胶料相当。连续混炼法可将能耗降低到原来的1/3。与对比胶料相比,连续混炼胶料的门尼粘度较高这一问题在进一步的研究中将通过优化工艺参数,以及采用充油的白炭黑填充RFC来解决。
参考文献:
[1] V. Eswaran,C. Kiehl,F. Magnus.Continuous mixingof silica loaded elastomeric compounds [ P]. US5711904,1998-01-27.
[2] S. Luther,M. Bogun.Continuous mixing of silica filledrubber mixtures with a planetary roller extruder[J].kautschuk Gummi Kunststoffe, 2005, 58 (7-8): 371-375.